Anilox-telan kennojen tukkeutuminen on itse asiassa väistämättömin aihe anilox-telojen käytössä. Sen ilmenemismuodot jaetaan kahteen tapaukseen: anilox-telan pinnan tukkeutuminen (Kuvio.1) ja anilox-telasolujen tukkeutuminen (Kuvio. 2).
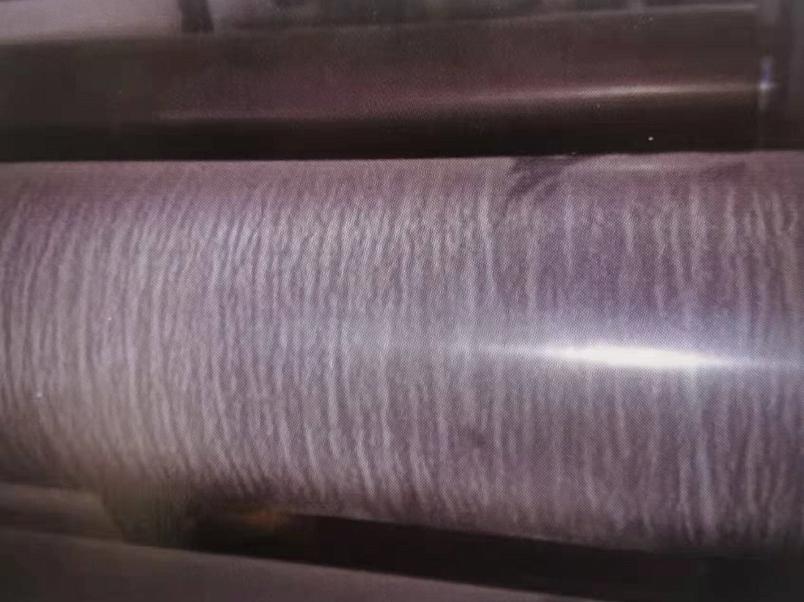
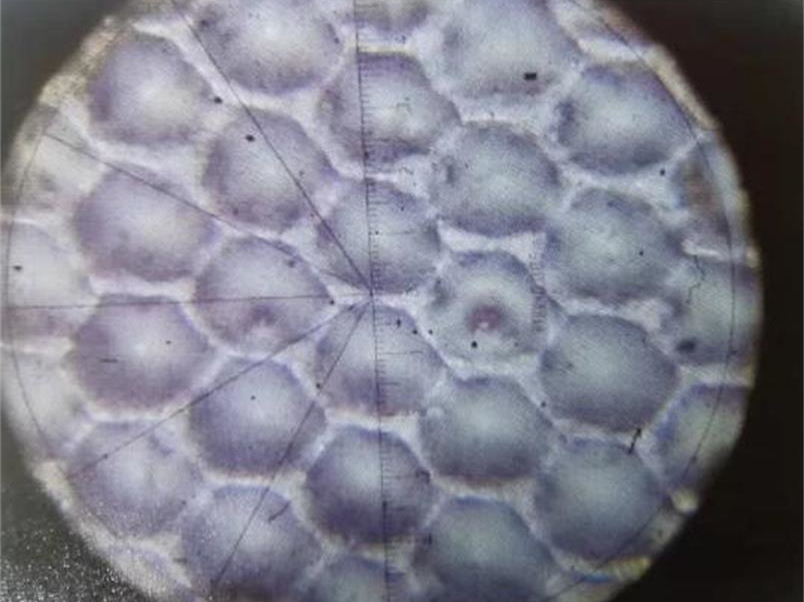
Kuva .1
Kuva .2
Tyypillinen fleksopainokoneen mustejärjestelmä koostuu mustekammiosta (suljetusta musteensyöttöjärjestelmästä), anilox-telasta, levysylinteristä ja alustasta. Korkealaatuisten tulosteiden aikaansaamiseksi on välttämätöntä luoda vakaa musteensiirtoprosessi mustekammion, anilox-telasolujen, painolevyn pisteiden pinnan ja alustan pinnan välillä. Tässä musteensiirtoreitissä musteen siirtonopeus anilox-telalta levyn pinnalle on noin 40 % ja musteen siirtyminen levyltä alustalle noin 50 %. Voidaan nähdä, että tällainen musteensiirto ei ole yksinkertainen fyysinen siirto, vaan monimutkainen prosessi, johon kuuluu musteen siirto, musteen kuivuminen ja musteen uudelleenliukeneminen. Fleksopainokoneen tulostusnopeuden kasvaessa tämä monimutkainen prosessi ei ainoastaan monimutkaistu, vaan myös mustereitin siirtymisen vaihteluiden taajuus kasvaa. Myös reikien fysikaalisille ominaisuuksille asetetaan yhä korkeammat vaatimukset.
Ristisilloitusmekanismilla varustettuja polymeerejä käytetään laajalti musteissa, kuten polyuretaanissa ja akryylihartsissa, parantamaan mustekerroksen tarttuvuutta, kulutuskestävyyttä, vedenkestävyyttä ja kemikaalien kestävyyttä. Koska musteen siirtymisnopeus anilox-telan soluissa on vain 40 %, suurin osa solujen musteesta jää itse asiassa solujen pohjalle koko tulostusprosessin ajan. Vaikka osa musteesta vaihdettaisiin, on helppo saada muste täydentymään soluissa. Hartsin ristisilloitus tapahtuu alustan pinnalla, mikä johtaa anilox-telan solujen tukkeutumiseen.
On helppo ymmärtää, että anilox-telan pinta on tukossa. Yleensä anilox-telaa käytetään väärin, jolloin muste kovettuu ja silloittuu anilox-telan pinnalle, mikä johtaa tukoksiin.
Anilox-telojen valmistajille keraamisen pinnoitusteknologian tutkimus ja kehitys, laserlevitysteknologian parantaminen ja anilox-telojen kaiverruksen jälkeisen keraamisen pintakäsittelyteknologian parantaminen voivat vähentää anilox-telojen solujen tukkeutumista. Tällä hetkellä yleisesti käytettyjä menetelmiä ovat verkkoseinän leveyden pienentäminen, verkon sisäseinän sileyden parantaminen ja keraamisen pinnoitteen tiiviyden parantaminen.
Painoyrityksille musteen kuivumisnopeutta, liukoisuutta ja etäisyyttä kumilastan ja painopisteen välillä voidaan myös säätää anilox-telasolujen tukkeutumisen vähentämiseksi.
Korroosio
Korroosiolla tarkoitetaan pistemäisten kohoumien muodostumista anilox-telan pinnalla, kuten kuvassa 3 on esitetty. Korroosion aiheuttaa puhdistusaine, joka tunkeutuu pohjakerrokseen keraamista rakoa pitkin, syövyttää pohjassa olevaa metallista pohjatelaa ja rikkoo keraamisen kerroksen sisältäpäin, mikä vahingoittaa anilox-telaa (kuva 4, kuva 5).
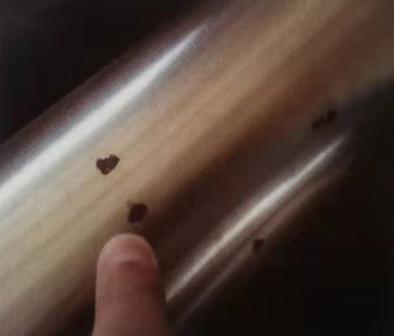
Kuva 3
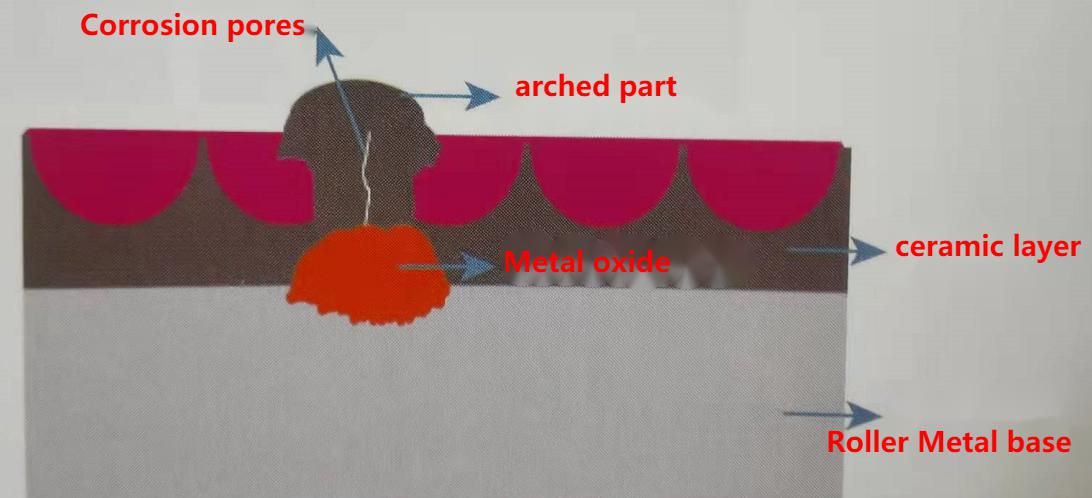
Kuva 4
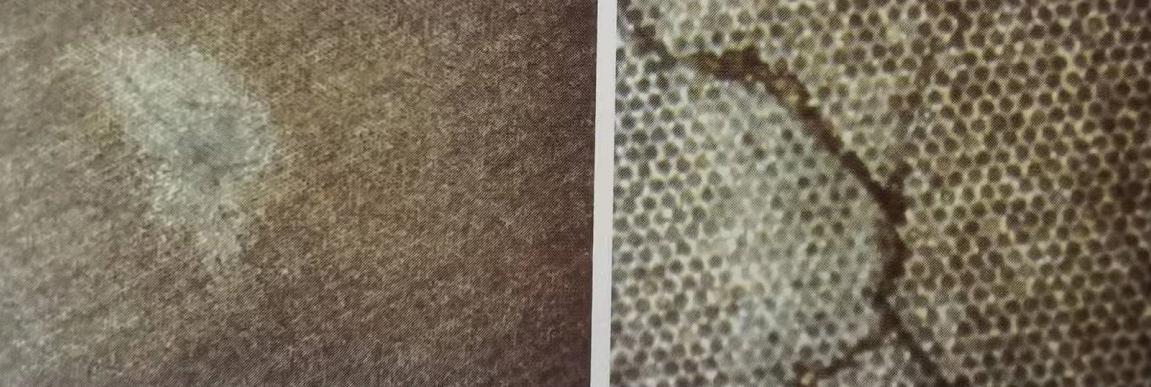
Kuva 5 korroosio mikroskoopilla
Korroosion muodostumisen syyt ovat seuraavat:
① Pinnoitteen huokoset ovat suuret, ja neste voi päästä pohjatelaan huokosten kautta aiheuttaen pohjatelan korroosiota.
② Puhdistusaineiden, kuten vahvojen happojen ja emästen, pitkäaikainen käyttö ilman oikea-aikaista suihkuttelua ja ilmakuivausta käytön jälkeen.
③ Puhdistusmenetelmä on väärä, erityisesti laitteiden pitkäaikaisessa puhdistuksessa.
④ Säilytysmenetelmä on väärä, ja sitä säilytetään kosteassa ympäristössä pitkään.
⑤ Musteen tai lisäaineiden pH-arvo on liian korkea, erityisesti vesipohjaisen musteen.
⑥ Anilox-telaan kohdistuu iskuja asennuksen ja purkamisen aikana, mikä johtaa keraamisen kerroksen raon muuttumiseen.
Alkuvaihe jää usein huomiotta, koska korroosion alkamisen ja aniloxtelan lopullisen vaurioitumisen välillä on pitkä aika. Siksi, kun keraamisen aniloxtelan pussistumisilmiö on havaittu, on otettava yhteyttä keraamisen aniloxtelan toimittajaan ajoissa holvikaaren syyn selvittämiseksi.
Ympärysmittaiset naarmut
Anilox-rullien naarmut ovat yleisimpiä anilox-rullien käyttöikää vaikuttavia ongelmia.()kuva 6)Tämä johtuu siitä, että aniloxtelan ja kaavinterän väliset hiukkaset paineen vaikutuksesta rikkovat aniloxtelan pinnan keramiikan ja avaavat kaikki verkkoseinämät tulostussuunnassa muodostaen uran. Tulosteessa näkyy tummempia viivoja.
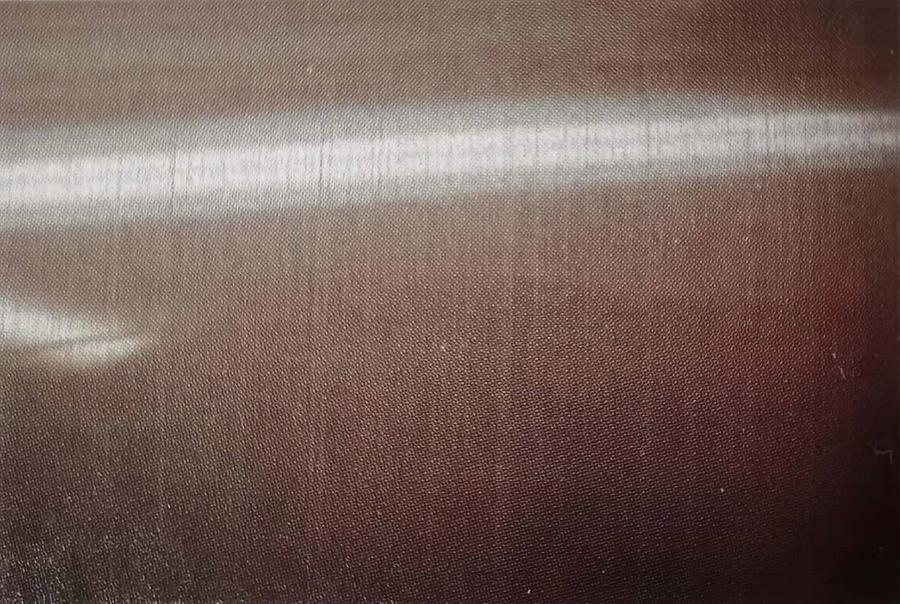
Kuva 6. Naarmuinen anilox-rulla
Naarmujen ydinongelma on kaavinterän ja anilox-telan välisen paineen muutos, jossa alkuperäinen pinta-pintapaine muuttuu paikalliseksi piste-pintapaineeksi. Suuri tulostusnopeus puolestaan nostaa painetta jyrkästi, jolloin tuhovoima on hämmästyttävä (kuva 7).
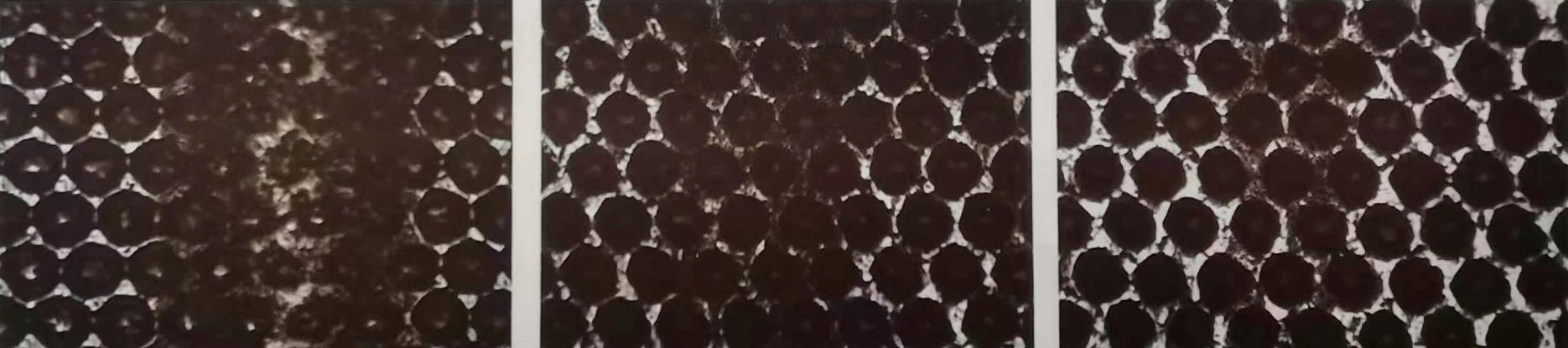
Kuva 7 vakavia naarmuja
Yleiset naarmut
pieniä naarmuja
Yleensä tulostusnopeudesta riippuen tulostusta haittaavat naarmut muodostuvat 3–10 minuutissa. Tähän paineeseen vaikuttaa monia tekijöitä, pääasiassa useista eri näkökohdista: itse anilox-tela, kaavinteräjärjestelmän puhdistus ja huolto, kaavinterän laatu, asennus ja käyttö sekä laitteen suunnitteluvirheet.
1. itse anilox-tela
(1) Keraamisen anilox-telan pintakäsittely ei ole riittävä kaiverruksen jälkeen, ja pinta on karkea ja helppo naarmuttaa kaavin ja kaapimen terä.
Kosketuspinta anilox-telan kanssa on muuttunut, mikä lisää painetta, moninkertaistaa paineen ja rikkoo verkon suurnopeuskäytössä.
Kohokuvioidun telan pintaan muodostuu naarmuja.
(2) Kiillotus- ja hienohiontaprosessin aikana muodostuu syvä kiillotusviiva. Tämä tilanne esiintyy yleensä anilox-telan toimituksen yhteydessä, eikä kevyesti kiillotettu viiva vaikuta painatukseen. Tässä tapauksessa painatuksen tarkistus on suoritettava koneella.
2. kaavinteräjärjestelmän puhdistus ja huolto
(1) Huonosti tasoitettu kammiokaavin aiheuttaa epätasaisen paineen riippumatta siitä, onko kammiokaavin terän taso korjattu. (kuva 8)
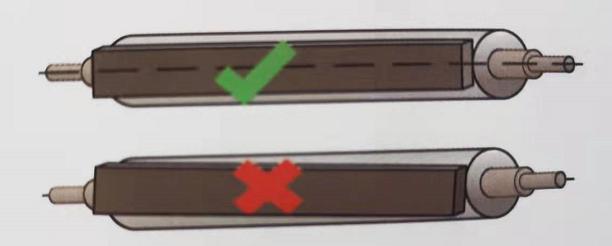
Kuva 8
(2) Olipa kaavinterän kammio pystysuorassa, ei-pystysuora mustekammio lisää terän kosketuspintaa. Se vahingoittaa suoraan anilox-telaa. Kuva 9
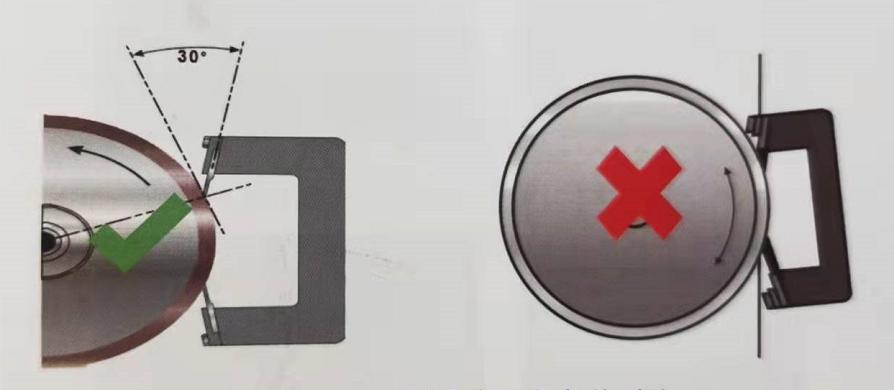
Kuva 9
(3) Kammion kaavinterän järjestelmän puhdistaminen on erittäin tärkeää. Estää epäpuhtauksien pääsyn mustejärjestelmään ja estää paineen muutoksia, jotka voivat juuttua kaavinterän ja anilox-telan väliin. Kuiva muste on myös erittäin vaarallista.
3. Kaavinterän asennus ja käyttö
(1) Asenna kammion kaavinterä oikein varmistaaksesi, että terä ei ole vaurioitunut, terä on suora ilman aaltoja ja sopii täydellisesti teränpitimeen, kuten
Kuten kuvassa 10 on esitetty, varmista, että paine pysyy tasaisena aniloxtelan pinnalla.
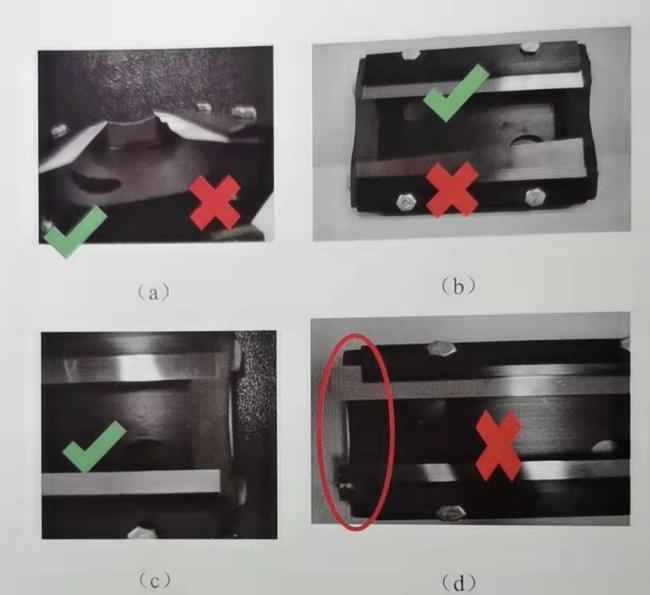
Kuva 10
(2) Käytä korkealaatuisia kaapimia. Korkealaatuisella kaavinteräksellä on tiivis molekyylirakenne kulumisen jälkeen, kuten kuvassa 11 (a) on esitetty. Hiukkaset ovat pieniä ja yhtenäisiä; heikkolaatuisen kaavinteräksen molekyylirakenne ei ole riittävän tiivis ja hiukkaset ovat kulumisen jälkeen suuria, kuten kuvassa 11 (b) on esitetty.
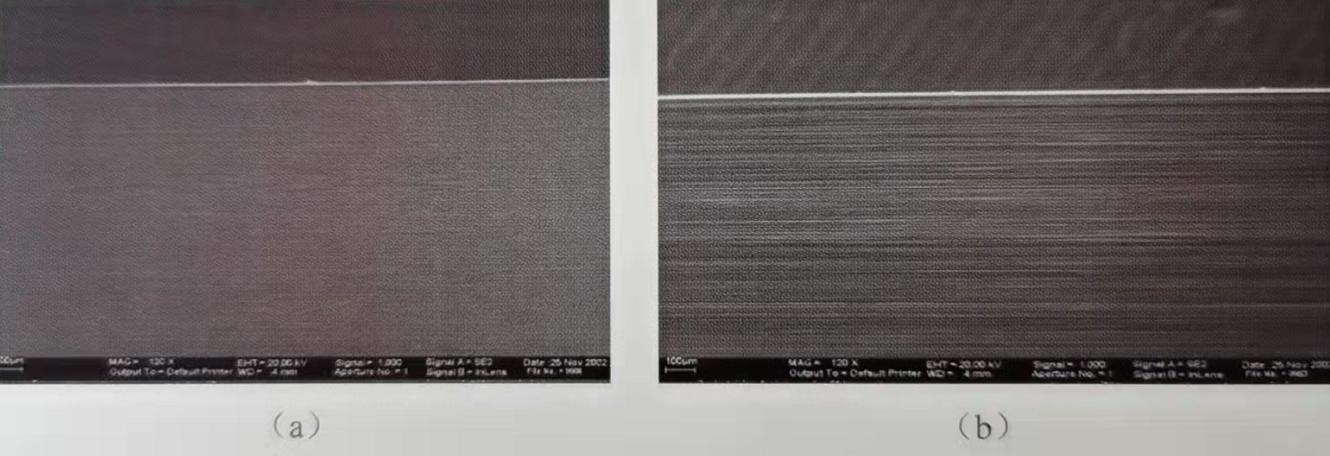
Kuva 11
(3) Vaihda teräveitsi ajoissa. Vaihdossa on tärkeää suojata veitsen terää kolhuilta. Kun vaihdat aniloxtelan rivinumeroa, sinun on vaihdettava myös teräveitsi. Eri rivinumeroilla varustettujen aniloxtelojen kulumisaste on epätasainen, kuten kuvassa 12 näkyy. Vasen kuva on matalan rivinumeron seula. Teräveitsen hionta teräveitsellä. Vaurioituneen päätypinnan kunto. Oikea kuva näyttää korkean rivinumeron omaavan aniloxtelan kuluneen päätypinnan kunnon teräveitseen nähden. Kaavinterän ja aniloxtelan välinen kosketuspinta, jonka kulumisaste on epätasainen, muuttuu, mikä aiheuttaa paineen muutoksia ja naarmuja.
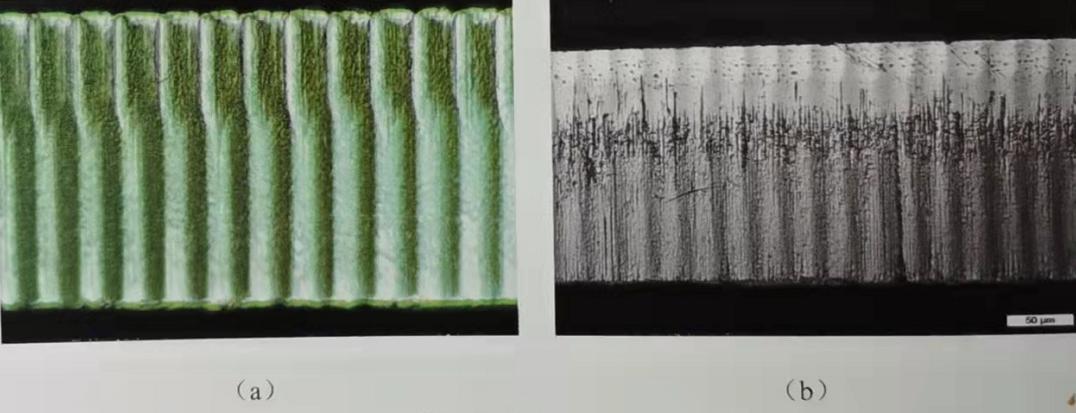
Kuva 12
(4) Imulastan paineen tulee olla kevyt, ja liiallinen paine muuttaa imulastan ja anilox-telan kosketuspinta-alaa ja kulmaa, kuten kuvassa 13 on esitetty. Epäpuhtaudet tarttuvat helposti, ja ne aiheuttavat naarmuja paineen muuttamisen jälkeen. Jos painetta käytetään kohtuuttoman paljon, vaihdetun kaapimen poikkileikkaukseen muodostuu kuluneita metallisia jälkiä (kuva 14). Kun kaavin irtoaa, se jää kaapimen ja anilox-telan väliin, mikä voi aiheuttaa naarmuja anilox-telaan.
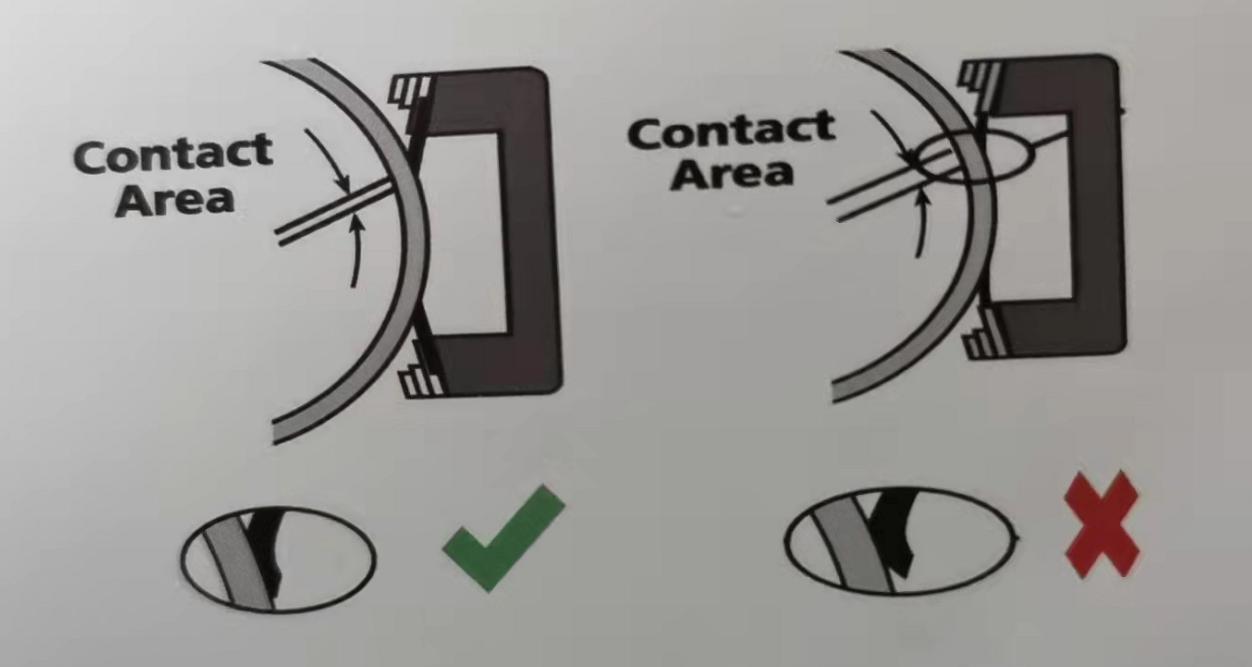
Kuva 13
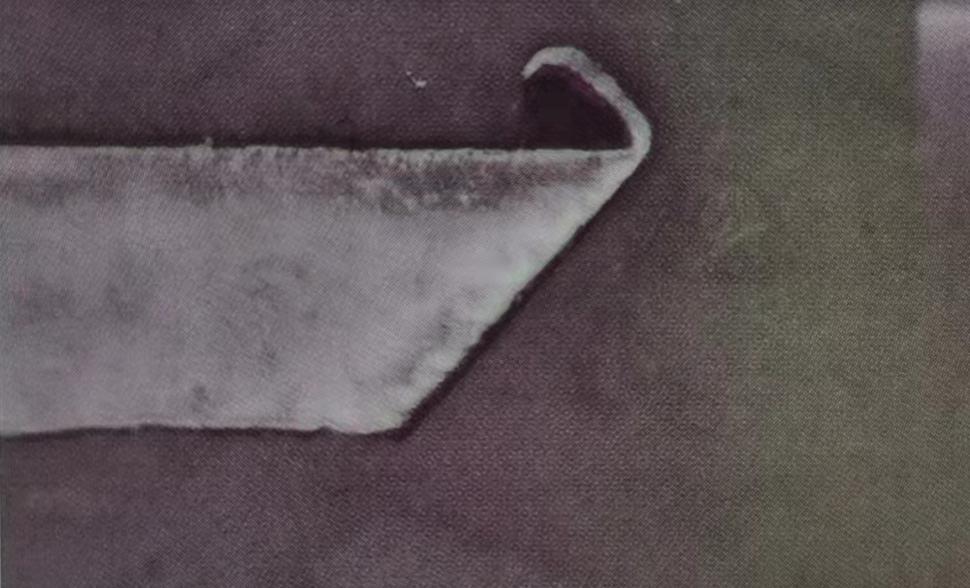
Kuva 14
4. laitteiden suunnitteluvirheet
Suunnitteluvirheet voivat myös aiheuttaa helposti naarmuja, kuten mustelohkon rakenteen ja anilox-telan halkaisijan välinen epäsuhta. Epävarmuustekijöitä ovat esimerkiksi kohtuuton imukupin kulman suunnittelu, anilox-telan halkaisijan ja pituuden epäsuhta jne. Voidaan nähdä, että anilox-telan kehän suuntaisten naarmujen ongelma on hyvin monimutkainen. Paineen muutosten huomioiminen, oikean puhdistuksen ja huollon suorittaminen, oikean kaapimen valinta sekä hyvät ja järjestelmälliset käyttötavat voivat merkittävästi lievittää naarmuuntumisongelmaa.
Törmäys
Vaikka keraamien kovuus on korkea, ne ovat hauraita materiaaleja. Ulkoisen voiman vaikutuksesta keraamit irtoavat helposti ja aiheuttavat kuoppia (kuva 15). Yleensä anilox-telojen lastauksen ja purkamisen aikana esiintyy kuoppia tai metallityökalut putoavat telan pinnalta. Pyri pitämään tulostusympäristö puhtaana ja vältä pienten osien pinoamista painokoneen ympärille, erityisesti mustelokeron ja anilox-telan lähelle. On suositeltavaa käsitellä anilox huolellisesti. Suojaa tela asianmukaisesti, jotta pienet esineet eivät putoa ja törmää anilox-telaan. Anilox-telan lastauksen ja purkamisen aikana on suositeltavaa kääriä se joustavaan suojapeitteeseen ennen käyttöä.
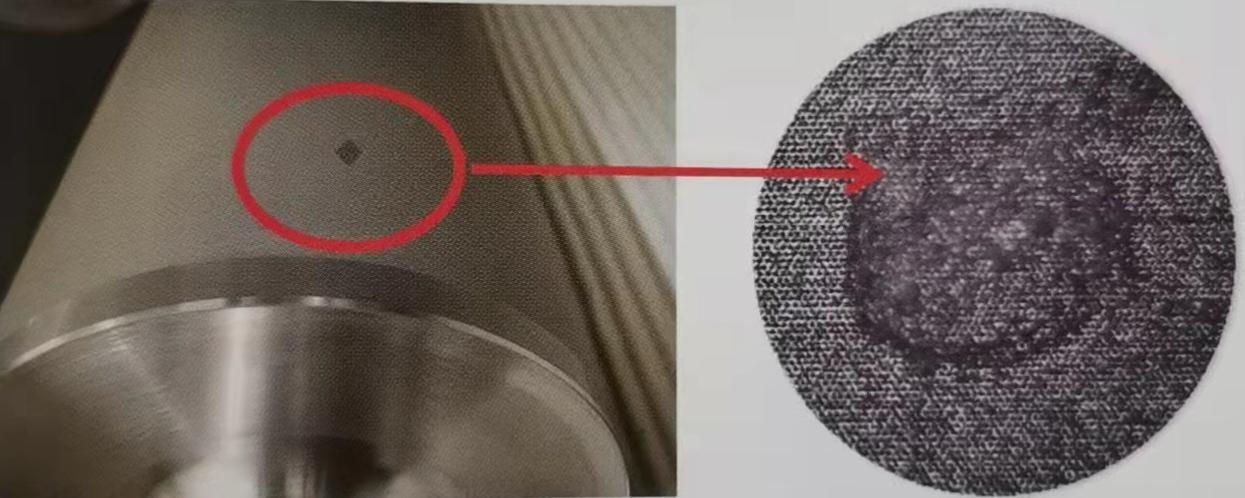
Kuva 15
Julkaisun aika: 23. helmikuuta 2022